(15)溶接からリベットに変更することで溶接歪みを解決する
精密板金において部品と部品を締結する、あるいは組み立てる場合によくある方法として溶接があります。一口に溶接と言ってもいわゆるアーク溶接からスポット溶接まで様々なものがありますが、いずれに方法でも熱を加えるという点からみると、歪みはどうしても生じてしまいます。特に、アルミのような溶接による歪みが発生しやすい材質は、TIG溶接などを行うと歪みが生じてしまいます。
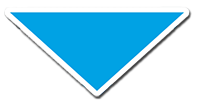
溶接の対象となる製品が、アルミなどで歪みやすい場合は、溶接によらない方法も検討してみると良いでしょう。ここではリベット留めをご紹介させて頂きますが、このリベット留めであれば熱を一切加えない締結方法であり、かつ生産性も高くなります。もし、対象となる製品が歪みが想定されて、水密・気密などの要求がなければリベット留めに変更することで大きな改善につながります。
その他関連するコストダウン事例
-
(1)切削加工から曲げ・溶接加工への工法変換でコストダウンを行う
【Before】
上記は真鍮を使った削り出し品です。真空に近い状態にまで引っ張ること、および強度的な問題からこれまでは真鍮のソリッドから削りだす、いわゆる機械加工品にて設計・製作を行っていました。切削加工は精密な加工ができる反面、余分な材料を購入しなければならない上に加工コストが高くなるので、コストダウンを行う際にも限界があります。
→解決事例を見る
-
(2)ハーフシャー(ダボ)を採用し位置決め時間を低減する
【Before】
精密板金においてスポット溶接を行う際や、あるいは溶接部品を取り付ける際、通常のケースでは位置決めを行う際にケガキを行ないます。しかし、組み立てる部品点数が多くなると、ケガキ自体の作業に時間を要してしまう上に、ケガキ線にしっかりと合わせる作業にも時間がかかってしまうので、コストアップにつながってしまいます。
→解決事例を見る
-
(3)精密板金の信頼性を上げるための板厚と溶接のポイント
【Before】
精密板金において溶接を行う際、板厚が厚い場合は大きな問題になりませんが、例えばステンレスなどひずみやすい材質で、かつ薄板を溶接する場合は1mm 未満の厚さになるとTIG 溶接では高い溶接技術を必要とされ、さらに熱による歪みが顕著になり、状況によっては溶接による穴が空くことがあります。
→解決事例を見る
-
(4)溶接付近の穴ピッチは寸法公差を緩和する
【Before】
上記のようなフレーム同士を溶接する場合においては、溶接の熱によって発生するひずみや収縮を考慮して設計を行い、寸法公差を入れる必要があります。例えば溶接を行うフレームにキリ孔が設けられており、この穴ピッチが± 0.1 mmだったとすると、溶接の熱によって発生するひずみ・収縮によって公差を達成することが困難となり、コストアップに繋がってしまいます。
→解決事例を見る
-
(5)強度が問題ない場合は不必要に溶接しない
【Before】
上記のような箱形状の精密板金を設計・製作する際に、四隅すべてに溶接の指示がされることがあります。すべての部分に溶接を行うことでその製品自体の強度は高くなりますが、かえって溶接による手間がかかったり、あるいは溶接によるひずみをとる作業が増えたりするので、本当にその溶接が必要なのか否かを十分に検討しておく必要があります。
→解決事例を見る
-
(6)精密板金におけるR 仕上げは「溶接R 仕上げ」を採用する
【Before】
精密板金でカバーなどの製作を行う場合、上記のような設計を行うと部品点数も増える上、加工に際しても曲げ工程に加えて溶接も2 箇所必要となり非常に手間がかかります。さらに、溶接部分が多くなることから、溶接の熱によるひずみも発生するので、特にひずみやすいステンレスやアルミの板ではひずみ取りや仕上げ工程に時間とコストがかかってしまいます。
→解決事例を見る
-
(7)溶接からリベット構造へ変換しサビ発生を防止する
【Before】
製缶板金におけるフレームのような製品や、あるいは精密板金でも、部品同士を固定する場合はその方法として溶接が採用されます。しかし、TIG 溶接やスポット溶接などは溶接の熱によってステンレスなどのフレームや板にひずみが発生する上、処理を行わないと上記の写真のようなサビが発生することがあります。
→解決事例を見る
-
(8)TIG 溶接からスポット溶接に変更しコストダウンを行う
【Before】
精密板金において、上記のようにステンレスの板同士を溶接する場合には通常TIG 溶接を行います。しかし、TIG 溶接を行う際には溶接の手間と仕上げに工数がかかり。コストアップの要因となってしまいます。さらに、2mm 以上の板厚であればあまり問題になりませんが、1mm 以下の薄物の溶接になると、作業者の技量によっては穴あきなどの不具合が発生することがあります。
→解決事例を見る
-
(9)スポット溶接を活用しコストダウンを行う
【Before】
箱形状のものを使った精密板金加工を行なう場合、上記のようなコの字を溶接するように設計すると、溶接の手間がかかる上、熱によってひずみが生じます。具体的には、溶接を行った裏面にひずみが生じ、表面が膨らんでしまいます。外観を重視するような医療機器や食品機械などの精密板金製品では、溶接の手間がかかる上に外観が損なわれてしまいます。
→解決事例を見る
-
(10)スポット溶接で溶接できるよう構造設計を行う
【Before】
水や油などを受けるパンなどを精密板金で製作する場合は、溶接方法の検討はもちろん、どのような部品で構成すれば一番水漏れが起こらないかの構造を検討する必要があります。上記のような構造で設計を行い溶接をしてしまうと、歪みが大きくなり、かつ修正が困難になります。水漏れ不可といった機器では溶接部から漏れが起こる可能性も否定できず、採用すべてきではありません。
→解決事例を見る
-
(11)スポット溶接は適正なピッチ幅を確保する
【Before】
TIG 溶接などの溶接よりも作業時間が短縮でき、さらに見た目も綺麗に仕上がるスポット溶接は、TIG 溶接に比較すると多少強度が落ちます。そのため、スポット溶接を採用する際には、精密板金製品の強度を向上させるためにスポット溶接の位置を図面上で指示されることがありますが、スポット溶接の間隔があまり狭すぎると分流が発生し溶接を行うことができなくなります。
→解決事例を見る
-
(12)角窓を溶接する際にはアングル材を使用する
【Before】
精密板金の設計・製作において、コストダウンを行う上でまず見直すべきは、いかに溶接を少なくするか、ということです。たとえば上記のような角窓形状を板金で製作する場合は、角窓部をすべて溶接しなければなりません。その結果、ひずみが生じてしまいひずみ取りと仕上げ工数が多くかかってしまうので、作業時間が増大し結果的にコストが高くなってしまいます。
→解決事例を見る
-
(13)ハンダ・ロウ付けを採用しピンホールの発生を防止する
【Before】
板厚が1mm以下の薄い材料は、溶接を行うと穴が空いてしまうことがあります。仮に、穴を空けることなく溶接ができたとしても、形状によってはピンホールが発生してしまいます。また、SECC(電気亜鉛メッキ鋼板)などのような材料は亜鉛が気化して穴が空き、ピンホールが発生しやすいです。このような場合、液漏れ・空気漏れが不可であれば、不具合となってしまいます。
→解決事例を見る
-
(14)溶接から接着に変更し外観の向上とコストダウンを行う
【Before】
ヘアライン加工されたステンレス材のカバー等に、スタッドなどの部品を結合する場合、溶接を指示されることがあります。しかし、ステンレス材のカバーは板厚が薄く、溶接を行うと必ずと言っていいほど装飾面の変形や変色が発生します。仕上げに時間がかかり、コストアップしてしまいます。
→解決事例を見る
-
(15)溶接からリベットに変更することで溶接歪みを解決する
【Before】
精密板金において部品と部品を締結する、あるいは組み立てる場合によくある方法として溶接があります。一口に溶接と言ってもいわゆるアーク溶接からスポット溶接まで様々なものがありますが、いずれに方法でも熱を加えるという点からみると、歪みはどうしても生じてしまいます。特に、アルミのような溶接による歪みが発生しやすい材質は、TIG溶接などを行うと歪みが生じてしまいます。
→解決事例を見る
-
溶接加工から曲げ加工への変更によるコストダウン
【Before】
2枚のステンレス材を組み立てる場合に溶接が採用される場合があります。この溶接するステンレス材の板厚が薄い場合は溶接を行うと必ずと言っていいほど、変形や変色が発生します。結果的に仕上げ加工に時間がかかりコストアップにつながります。
→解決事例を見る
-
コーキングを活用して溶接箇所を減らし、歪みの発生を抑える
【Before】
ステンレス材のカバー等を製作する場合、全周溶接が指示される場合があります。しかし、ステンレス材のカバー等は、板厚が薄く、溶接を行うと、高確率で歪みや変色が発生します。その結果、仕上げに時間がかかり、コストアップに直結します。
→解決事例を見る
-
『鋳物+フライス加工』から『板金加工』への工法転換により、コストダウンを行う
【Before】
上記画像の製品は、アルミ鋳物へのフライス加工により製作されておりました。当工法は、数量が多い場合に最適な加工方法です。また、当工法では、型が必要となり、型製作のみで2か月の期間を要する場合があります。そのため、ロット数が少ない場合や製作を急いでいる場合、この加工方法を選定することは適切とはいえません。
→解決事例を見る
-
リブ溶接で補強する箇所を、三角リブにより代用しコストダウン
【Before】
筐体やカバー、架台の製作おいてTigやMig、ファイバーレーザなどの溶接加工を必要とする製品は多くあります。その中でも高い強度を求められる製品の場合は、一般的にリブ溶接が用いられます。 リブ溶接による接合は、強度を持たせるための接合方法の一つですが、その他の接合方法と比較しても加工コストは高くなってしまいます。 当社のお客様からも、接合コストを上げずに、強度を持たせる加工方法はないか、と相談をいただきます。
→解決事例を見る