精密板金とは
【目次】
1. 精密板金とは
精密板金とは、板金加工の一種であり、通常の板金加工と比較し高い加工精度・寸法公差が要求される製品を専用の機械などを使い加工することを指します。
医療機器、食品機器、半導体装置や光学機器などが精密板金で加工される主な製品です。
精密板金では、その他板金加工と同様に金属板に曲げ・抜き・溶接・切断などの加工を施します。
精密板金の特徴は、精度の高さ、複雑な形状の加工にも対応できる、小ロットでの生産に向いているなどがあげられます。
精密板金の方法で加工される製品の代表例には、医療機器や食品機器、半導体装置、光学機器などがあげられます。これらの製品はその用途から緻密さや精度が必要であるため、通常の板金加工ではなく、精密板金加工による加工を施す必要があります。
多くの精密板金加工の場合、設計から組み立て作業までを一括して行うため、筐体製作では中に組み込まれる機器や装置とのバランスを意識した加工・仕上げが可能で、見た目にも美しく仕上がります。
また、精密板金ではプレス板金で加工する時よりもイニシャルコストを抑えることができます。
プレス板金で加工する際は専用の金型が必要となりその分コストがかかるのですが、精密板金では汎用金型を活用することにより、コストダウンを実現することができます。
しかしながら、精密板金にも弱みがあります。
金型の費用がかからないので試作や少量生産には向いていますが、数千個におよぶような大量生産には向いていません。
1~1000個までの小~中ロットでの試作や複雑な形状の製品の加工については精密板金、単純な形状の製品の大量生産についてはプレス加工といったように、その製品・生産量によってそれぞれに適した加工を依頼するのが良いと考えられます。
>>試作板金についてお悩みの方はこちら
2. 精密板金と板金の違い
板金加工は、以下のように分類することができます。
- ・自動車板金
- ・建築板金
- ・工場板金
自動車板金
一般的に自動車板金での加工は打ちだし板金やたたき板金と呼ばれます。自動車のボディーのキズや凹みを修理するときに行われる自動車板金加工では、精密板金と同じように金属の板を曲げ・溶接などの加工を施すのですが、ボディーの凹みを叩いたりパテを使い細かい凹凸を修正したりすることが主な加工です。
一般的に自動車板金での加工は打ちだし板金やたたき板金と呼ばれます。
建築板金
金属板を曲げる加工・延ばす加工を施し、主に屋根・外壁・雨といなど住宅の外装に関する製品を製作します。
外観やデザインなどにこだわり加工する必要があるので美的センスや繊細さが求められます。
工場板金
一般的にスマートフォンや家電製品の筐体など私たちの日常で頻繁に目にするものは工場板金によって製作されています。
主に工場で板金加工を施していることから工場板金と呼ばれています。
精密板金は工場板金に分類されます。
工場板金の中でも、上述したような医療機器や半導体、光学機器などの繊細な加工が必要なものは精密板金加工によって製作されます。
また、精密板金は、プレス機やレーザー加工機、ターレットパンチプレスなど特殊な機械によって加工をするという特徴もあります。
精密板金とよく比較される技術がプレス板金です。プレス板金は、製作する部品に合わせて専用の金型を起こし、成形する板金加工です。プレス板金は一度金型を起こしてしまえば、複雑な形状でも精度の振れ幅が少ない加工が出来るため量産に最適。しかし金型の製作に、4~6週間の納期と数十万~数百万円の費用がかかってしまいます。対して精密板金は、プレス板金に若干精度が劣るものの、1~2週間の納期と数万円程度の費用で製作が可能。そのため個数が少ない製品や試作・開発段階での製作に最適な板金加工です。
このように、精密板金は他の板金加工と違う点を多く持つため精密板金加工ができる企業や業者も限られてきます。
3. 精密板金が活躍する様々な業界
精密板金によって加工され出来上がった製品は、様々な業界で使用されています。
例えば会社や工場で使用されているロッカーなどの箱物は、すべて一枚の板に精密板金加工を施して製作されています。使用される材質はステンレス・アルミ・鉄などの材料が多く使用されており、使用される環境や用途によって使用される材料も最適なものが選ばれています。
例えば、ステンレスは医療機器や食品機械、あるいは半導体製造装置などの業界で多く用いられますし、鉄系のものは一般家電・OA製品、あるいは工作機械などの産業機械で多く採用されています。アルミについては用途が限定されますが、軽量かつ剛性が高いという理由から、航空機や人工衛星などの航空宇宙分野などの分野で採用される事例が増えています。
医療機器
食品
エネルギー・半導体
光学機器・OA機器
その他
>>製品事例一覧はこちら
4. 精密板金における様々な加工方法
精密板金加工では、鉄やステンレス、アルミなどの金属・非鉄金属の一枚の板から製品を立体的に作り上げます。
そのため、目的とする形状に仕上げるために、加工方法としては大きく「抜き加工」「曲げ加工」「溶接加工」「組立」という4つの加工方法に分類することができます。
これらの方法は下記で説明するような様々な機器を用いて加工されます。
4-1. 抜き加工とは?
抜き(ブランク)加工は、レーザーや汎用金型を使って材料の金属板から任意の形状を抜き落とす加工です。
レーザーを使う機械をレーザー加工機、汎用金型を使う機械をターレットパンチプレスと呼び、用途別に使い分けます。また最近ではレーザーと汎用金型、両方の加工が出来る複合加工機も増えてきました。
レーザー加工
レーザー加工はファイバーレーザー加工とCO2レーザー加工の2種類があり、レーザーは主に外形や大きな穴の抜き落としに使用され、レーザーの熱で金属を溶かして切断します。
ファイバーレーザーは、光ファイバーを使用した加工精度と加工速度が特徴のレーザー加工です。
近年レーザー加工の主流となっています。
対してCO2レーザーは、その名の通り炭酸ガス(CO2)を使用したレーザーです。加工精度や加工速度はファイバーレーザーに劣りますが、機械本体の安さが特徴です。
汎用金型を使った加工
汎用金型は主に小さな穴の抜き落としに使用され、パンチとダイで挟み込んで金属を切断します。汎用金型による抜き加工は、レーザーに比べて切断面の美しさが特徴。レーザーでは切断面に焼けた跡が残ってしまうのに対し、金型では切断面の美しい抜き加工が可能です。
汎用金型では、ターレットパンチプレス(タレパン)と呼ばれる機械で加工を行います。タレパンは円盤状のターレットに金型を装着後、作業台に載せた材料を金型で加工。さらにタレパンには複数の金型を同時に装着できるため、形状の異なる穴がある場合でも一度に加工できます。穴の位置や個数は、レーザーと同様に事前に段取りしたプログラムで制御するため、材料を載せた後は自動で加工が行われます。
複合加工機での加工
さらに近年では、レーザーと汎用金型を使った抜き加工を同時にできる複合加工機も登場しました。複合加工機もレーザー加工機やタレパンと同様にプログラムで制御できるため、材料を載せてからは自動で加工が可能です。また当社が保有している複合加工機LC-2012C1NTでは、レーザーと汎用金型を使った抜き加工だけでなくネジ穴を空けるタップ加工も同時に加工可能。標準的なねじの規格であるM1~M6までのタップ加工と、バーリングと呼ばれる穴の周辺を立ち上げる加工が可能です。
当社の複合加工機では、抜き加工だけでなくタップ加工やバーリング加工まで同時に加工可能です。工数削減により、コストダウンや納期の短縮が可能です。
4-2. 曲げ加工とは?
曲げ加工とは、金属板に高重量の圧力をかけて90度や45度に曲げる加工で、ベンディング加工とも呼ばれます。
曲げ加工ではプレスブレーキと呼ばれる機械で、金型を使って金属を加工します。
またプレスブレーキには使用する金型や曲げ方に種類があり、一般的な角度曲げそれらを駆使して曲面上に曲げるR曲げや、折り畳むように曲げるヘミング曲げなどの成形が可能です。
さらに当社では、幅広いサイズの曲げ加工に対応可能。サイズの異なる5台のプレスブレーキを保有し、1cmの小型の製品から3mの大型の製品まで曲げ加工が出来ます。
角度曲げ
精密板金の最も一般的な曲げ加工が、金属板を90度や45度に曲げる加工。パンチとダイで金属板を挟み、少しずつパンチを下げて金属板をV字に曲げ、任意の角度に成形します。そして正確に曲げるために重要なのが、パンチを下げる距離の見極め。しかし曲がる角度とパンチを下げる距離の関係は、金属の種類と厚みで一意には定まりません。実は同じ金属でも材料ごとに、合金の含有物の割合の違いや場所ごとの偏りが存在し、これがパンチを下げる距離に影響します。そのため曲げ加工は機械による自動化が難しく、当社でも製品1つ1つを職人の手で加工しています。
R曲げ
R曲げは金属板を曲面上に曲げる加工。R曲げは安全性やデザイン性を目的に、箱型製品の角を丸めるためによく利用されます。R曲げをする方法は、先端が丸いR曲げ用の金型を使用する方法と位置をずらしながら数度ずつ曲げていく方法の2種類。通常は、半径の小さなR曲げではR曲げ用の金型を使用する方法が、半径の大きなR曲げでは位置をずらしながら数度ずつ曲げていく方法が採用されます。
ヘミング曲げ
ヘミング曲げは金属板を折り畳むように曲げる加工。折り畳むことにより切断面を隠せる安全性や厚みを2倍に出来る強度などを目的に利用されます。ヘミング曲げは、金属板を鋭角に曲げる工程と、鋭角に曲げた部分を押しつぶす工程の2工程で加工。鋭角に曲げる工程では先の尖ったパンチを、押しつぶす工程では先が平らなパンチを使用します。
4-3. 溶接加工とは?
溶接加工は熱などで金属を溶かし、金属同士を接合する加工です。溶接加工には多くの種類があり、大きく分けると融接・圧接・ろう接の3つ。さらに、融接の中にはTIG溶接やレーザー溶接、圧接の中にはスポット溶接など、様々な溶接法が含まれています。
アルミ溶接加工事例
-
アルミ溶接加工品(TIG溶接)
-
アルミ溶接カバー(t1.0mm)
-
アルミ筐体(t=2.0mm)
-
アルミ薄板溶接(溶接仕上げレス)
-
アルミ薄板筐体(t=1.5mm)
-
アルミ溶接カバー(黒アルマイト仕上げ)
-
アルミ薄板溶接カバー
-
アルミ溶接フレーム
>>アルミの溶接専用サイトはこちら
融接
融接は溶接する金属の溶接部分を熱で溶かして接合する溶接。融接は熱の発生方法で種類が分かれ、気体中の放電現象を利用するのがアーク溶接、レーザーの熱を利用するのがレーザー溶接です。
・TIG溶接
気体中の放電現象を利用するアーク溶接の中で、代表的な溶接方法がTIG溶接です。
TIG溶接は、タングステンを使ったアーク溶接です。TIG溶接は、ほとんどの金属を溶接できる点が特徴。鉄・ステンレス・アルミなどの使用頻度の高い金属から、銅・チタンなどの使用頻度の少ない金属まで溶接可能です。
・ファイバーレーザー溶接
レーザー光線の熱を利用するレーザー溶接の中で、代表的な溶接方法がファイバーレーザー溶接です。
ファイバーレーザー溶接は、光ファイバーを使ったレーザー溶接です。ファイバーレーザー溶接は、溶接熱による歪みの少なさが特徴。一般に板厚の薄い材料やアルミなどの熱に弱い材料を溶接すると、溶接の熱によって歪みが発生します。しかしファイバーレーザー溶接では、溶接箇所に短時間で集中的に熱を加えることが可能。溶接する金属に余分な熱を与えないため、歪みの少ない溶接ができます。
・Co2レーザー溶接
Co2レーザー溶接とは、「炭酸ガスレーザー溶接」とも呼ばれ、レーザー溶接の中でも、ごく一般的に使用されている溶接の種類になります。CO2レーザ溶接は、装置の高出力化が比較的容易であり、連続発振で中厚板までの溶接加工に使用されています。10.6μmという長波長を出力することが可能なため、狭い範囲で深く溶け込む溶接が行えることから、作業効率よく溶接を行えることが特徴的です。
圧接
圧接は溶接する金属の溶接部分に圧力と熱を加えて接合する溶接。圧接は、圧力と熱を加える方法で種類が分かれ、中でも代表的な方法が電流で熱を発生させるスポット溶接です。
スポット溶接は、電流で発生する熱を利用した溶接。スポット溶接では、溶接する金属同士を電極で挟み圧力を加え、電流を流した時に発生する熱で溶接します。スポット溶接の特徴は、溶接速度の速さ。溶接箇所が線ではなく、点のため短時間で溶接が可能です。
4-4. 精密板金との違いに注意!プレス加工
また、精密板金とよく間違われやすいものにプレス加工による板金というものがあります。
プレス加工も精密板金加工同様金属の板を切るところからスタートしますが、その次に使う金型・その後の加工によって違いが生まれてきます。
プレス加工が専用の金型を使い大量生産するものに向いているのに対して、精密板金加工では、汎用の金型とターレットパンチプレスやレーザー加工機、あるいはベンディングマシーンなどの専用の機械を使い加工をしていきます。
このように、精密板金は、専用の機械をそれぞれの製品に合わせ丁寧に作っていきます。
このことから、精密板金加工では、試作や小ロットの製作に向いていることが分かります。
5. 精密板金で使用される様々な加工機器
精密板金加工では、「抜き」・「曲げ」・「溶接」・「組立」などを行うために様々な設備が必要です。それらを大きく分けると、”抜き”を行う「レーザー加工機」と「ターレットパンチプレス」、”曲げ”を行う「プレスブレーキ (ベンダー)」、”溶接”を行う「溶接機」”組立”を行う「組立機」があります。
5-1. レーザー加工機
レーザー加工機は「レーザー光線」を切断したい部分にあてることで、切断したい部分を局所的に 溶融させます。その溶融した部分にアシストガスを噴出し、溶融部を噴き飛ばし切断します。レーザー加工機での加工は素材に触れることなく加工できます。 レーザー加工機はレーザーを自由にあてることができ、精密板金で扱われるような素材のステンレスや複雑な形状の製品の加工・厚い板厚の鋼板を切断することに適しています。
また、レーザー加工機は、加工精度や切断面がきれいになるという強みがあるため、精密板金において大きな役割を担っています。
■パンチ・レーザー複合機 LC2515の紹介動画
5-2. ターレットパンチプレス
ターレットパンチプレスはプレス機械の1種で、様々な形状の金型を取り付けてあらかじめプログラミングされたNC装置により抜きうち加工をします。抜きたい穴の形状と金型の形状が一致する場合は一回の加工のみで加工が完了します。 異なる形状の場合も汎用金型を用いて追い抜きすることで目的の形状に加工します。レーザー加工機と比較して、短時間で加工することができます。
具体的には、カス上がりレス加工・ファインコンタリング加工・高速バリつぶし加工・スロッティング加工・高速成形加工、下向き成形加工・セーフティー・インチベンド加工・高速マーキング加工などしっかりと活用しながら、抜き加工(ブランク加工)を行っております。
5-3. プレスブレーキ(ベンダー)
プレスブレーキは抜き加工で切り出した板材を曲げるための機械です。下型・ダイと呼ばれる金型を固定し、上型・パンチと呼ばれる金型をダイに対して上下に押し込んで鋼材を曲げていきます。 この上下運動によって、生じる加圧の力と金型の組み合わせによって思い描く形状に加工することができます。形状によっては、金型が干渉するために曲げられない製品もあるので、うまく曲げ加工ができるように設計段階から注意をする必要があります。
■ベンディングマシン HD‐NTシリーズの紹介動画
5-4. 溶接機
溶接機は様々な部品を接合するための機械です。溶接機にも種類があり、TIG溶接機やCO2溶接機、スポット溶接機など様々な溶接機が存在しています。 溶接は、鉄ならばCO2溶接、ステンレスならばTIG溶接などと材料や板厚などによって溶接方法が変わってくるので、材質・板厚を考慮したうえで溶接機を選定する必要があります。
■ファイバーレーザー溶接機の紹介動画
6. 精密板金加工の工程
精密板金加工の加工工程は、加工工程・製品によって異なりますが、大まかな流れは以下のようになっています。
- 1.抜き加工(ブランク加工):金属板からレーザーなどで任意の形状を抜き落とす工程
- 2.バリ取り:バリ(抜き加工によって金属の切断部分に生じたトゲ)を取り除く工程
- 3.曲げ加工(ベンディング加工):金属板に高重量の圧力をかけて曲げる工程
- 4.溶接加工:熱で金属を溶かし、金属同士を接合する工程
- 5.検査
その他にも製品によって、ネジ穴を開けるタップ加工、メッキや塗装などの表面処理なども行います。ちなみに精密板金の「精密」は高精度な加工を示す意味で、小さい物の加工する意味ではありません。自動車板金や建築板金に比べて高い精度が求められるため、精密板金と呼ばれています。
7. 精密板金のコストダウン方法とVA・VE事例
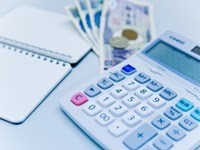
精密板金加工による製品を含め、いわゆる工業製品は様々な要素によってコストが決定します。そのコストを決定する要因は、大きく下記の4点に分けることができ、それぞれを考慮した上で設計を行うことが、精密板金におけるコストダウンに繋がります。
7-1. イニシャルコスト
一般的な板金、いわゆるプレスブレーキによる曲げや溶接ではイニシャルコストは殆ど掛かりませんが、絞りなどを行う際には基本的に金型が必要になります。
こうした場合は大きなイニシャルコストを必要としない簡易金型(ダイレスフォーミング)を採用できるような設計を行うと、金型にかかるイニシャルコストを抑えることができます。
複雑な形状の試作や小ロットの生産を行う際にはこのダイレスフォーミングを採用することがコストダウンに繋がります。
>>ダイレスフォーミングとは?
7-2. 材料の選定
2点目に、材料によるものが挙げられます。
精密板金の材料は金属です。
中でも主として使用されるのが『鋼鉄』、『ステンレス鋼』、『アルミニウム合金』です。
これらの金属は加工性に優れ、金属部品に適した性質を持ちます。
鋼鉄
鋼鉄は炭素を0.04%から2%程度含む鉄の合金で、ステンレス鋼と区別するために鉄と呼ばれます。精密板金で使用される代表的な金属で、他の金属に比べて安価なことが特徴。鋼鉄の中にも種類があり、精密板金でよく利用されるのが冷間圧延鋼板(SPCC)・電気亜鉛メッキ鋼板(SECC)の2つです。
SPCCは、柔らかく加工性に優れた点が特徴です。また鉄の中でも安価なのがよく利用される理由でもあります。しかし弱点として錆びやすい性質があるため、塗装やメッキでサビ対策をする場合が多いです。
SECCはSPCCに電気亜鉛メッキを施した鋼鉄でボンデ鋼板とも呼ばれます。
メッキにより錆びにくい点が特徴で、加工性はSPCCと同じため柔らかく加工しやすい。またメッキによって表面が均一になり、塗装性に優れている特徴もあります。
SPCC・SECC精密板金加工サービス

SPCC・SECCの精密板金におけるコストダウン設計のポイント
1.目的に応じて、最適な塗装方法を選択する
2.塗装範囲を明確に指示する
3.定尺を考慮した設計を行う
>>詳細はこちら
ステンレス鋼
ステンレス鋼は、クロムやニッケルを含んだ鋼鉄の合金で、ステンレスやステンと呼ばれます。ステンレスの最大の特徴は錆びにくさで、鉄のように錆を防止するための塗装やメッキが必要ありません。そのため錆びにくさの求められる、キッチンのシンクなどの水回りで使用されています。ステンレスの中にも種類があり、精密板金でよく利用されるのがSUS304とSUS430の2つです。
SUS304は、クロムとニッケルを含んだステンレスです。非常に性質の優れた金属、高い強度や耐熱性が特徴。加工性にも優れ、精密板金で最も使用されているステンレスです。
SUS430は、クロムのみを含んだステンレスです。SUS304と同様に非常に優れた性質を持っていますが、SUS304には少し及びません。しかしSUS304よりも低コストなため、性能に問題がない場合はSUS430に代用することでコストダウンを実現できます。
ステンレス精密板金加工サービス
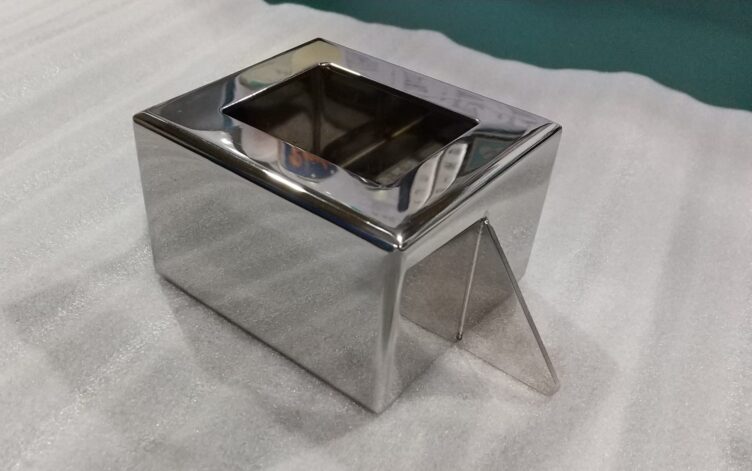
ステンレスの精密板金におけるコストダウンのポイント
1.溶接部分を最小限に減らす
2.定尺を考慮した設計を行う
3.同じ板厚の板材を採用する
>>詳細はこちら
アルミニウム合金
アルミニウム合金は、マグネシウムなどを含んだアルミニウムの合金で、アルミと呼ばれます。アルミの最大の特徴は軽さで、鉄やステンレスに比べて1/3程度の重さしかありません。そのため軽量化が求められるノートパソコンなどで使用されています。アルミの中にも種類があり精密板金でよく利用されるのが、マグネシウムを含んだA5052P。中程度の強度を持ち、耐食性や加工性に優れた金属です。
アルミ精密板金加工サービス
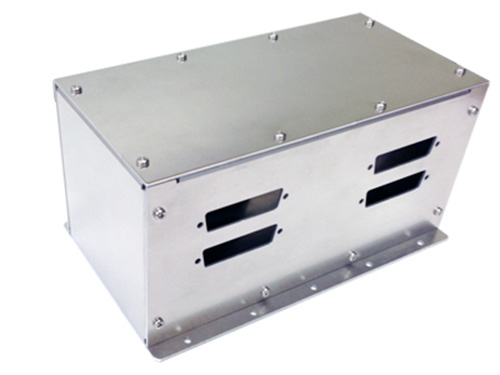
アルミの精密板金における設計のポイント
1.曲げRを考慮して設計を行う
2.歪みの発生しやすい溶接(TIG溶接等)を避ける
3.板厚が違うもの同士の溶接を避ける
>>詳細はこちら
精密板金の材料として使われる主な金属である、『鋼鉄』・『ステンレス鋼』・『アルミ合金』ですが、それぞれの金属の特徴は一長一短です。例えば、鉄はコスト、ステンレスはサビ対策が不要、アルミは軽いなどの特徴があります。そのため精密板金で部品を製作する場合は、使用用途に適した材料の選択が重要です。
また、材料選定段階でコストを抑えることもできます。
例えば精密板金では定尺と言われる決まった板の寸法がありますが、これを考慮して設計すればコストを抑えることができますし、さらに鉄とステンレスなど材質によっては定尺のサイズが異なるので、設計する際にはこのポイントを事前に織り込んでおくことが必要です。
7-3. 加工方法
次は曲げ・溶接などの加工方法です。精密板金で用いる材料には、板厚や材質によって曲げ限界に相違があったり、あるいは溶接しにくい構造や、グラインダーなどの溶接後の仕上げが必要になるような構造で設計を行うと、加工ができない、加工はできるが時間がかかりコストアップになる、といったことに繋がります。基本的には溶接はなるべくしないように設計することがポイントです。
7-4. 組立
精密板金加工による製品のコストダウンを追求するためには組立作業性を考慮した上で設計を行うことが必要です。図面上で描くことはできても、実際の組立の現場ではスパナを回すことができない、あるいは部材同士が緩衝して組みたてることができないといったことが発生することもしばしばあります。組立に要する作業時間と加工時間を合わせてトータル作業時間を低減させる設計を行うことがポイントです。
7-5. VA・VE事例
下記より精密板金加工の具体的なVA・VE事例をご紹介しておりますので、ご興味のある方は是非こちらもご覧ください。
VA・VE事例一覧
-
(1)小ロットの場合は簡易金型(ダイレスフォーミング)を採用する
【Before】
上記の写真のような丸・四角・長丸などの絞りを行う場合には、通常であれば一度金型を起こす必要があります。このような簡単な形状の絞りでも金型を起こせば50 万円程度のイニシャルコストがかかってしまう為、小…
→解決事例を見る
-
(2)簡易金型(ダイレスフォーミング)の採用でコスト低減と納期短縮を行う
【Before】
プレスや板金加工で簡単な絞りを行う際でも、通常であれば金型が必要となります。この金型はパンチとダイに分かれ、合わせて10万円程度となります、小ロットの場合や試作のみ対応する場合はこのイニシャルコストが…
→解決事例を見る
-
(7)簡易金型(ダイレスフォーミング)による絞りと追加工によってコストダウンを行う
【Before】
精密板金製品に絞り加工を行なう際には、プレス機、ターレットパンチプレス、あるいは簡易金型(ダイレスフォーミング)を用いて行われます。しかし、板厚が厚かったり、絞りの深さが深い場合には、工法が限られます…
→解決事例を見る
-
(1)切削加工からレーザー加工への工法転換でコストダウンを行う
【Before】
単純な形状のワークほど、本当に必要な面粗度を図面に記載することがコストダウンに繋がります。上記の図面ではワークの側面の面粗度が、機械加工を前提とした▽▽(三角ふたつ)の指示が入っています。図面において…
→解決事例を見る
-
(1)切削加工から曲げ・溶接加工への工法変換でコストダウンを行う
【Before】
上記は真鍮を使った削り出し品です。真空に近い状態にまで引っ張ること、および強度的な問題からこれまでは真鍮のソリッドから削りだす、いわゆる機械加工品にて設計・製作を行っていました。切削加工は精密な加工が…
→解決事例を見る
-
(3)精密板金の信頼性を上げるための板厚と溶接のポイント
【Before】
精密板金において溶接を行う際、板厚が厚い場合は大きな問題になりませんが、例えばステンレスなどひずみやすい材質で、かつ薄板を溶接する場合は1mm 未満の厚さになるとTIG 溶接では高い溶接技術を必要とさ…
→解決事例を見る
-
(3)流通性の高い材料、板厚の使用でコストダウンを行う
【Before】
機器を設計するにあたっては、求められる機能から材料を選択することが必要ですが、品質・機能とコストのバランスを取る場合には、材料のコストや入手性も考慮した上で選定を行わないとスムーズな立上げや量産を行な…
→解決事例を見る
-
(2)定尺を考慮した設計でコストダウンを行う
【Before】
ステンレスや鉄などの板材は定尺と呼ばれる決まった寸法があり、市場では基本的にはそれが元となり流通しています。たとえばステンレスを使った精密板金の製品を設計する場合、ステンレスはメーター板という1m ご…
→解決事例を見る
-
(6)切削加工品を簡易金型(ダイレスフォーミング)による絞り加工で置き換えるポイント
【Before】
切削加工を前提としている部品も、必要な機能を見極めることができれば簡易金型(ダイレスフォーミング)による精密板金製品に置き換えることで大幅なコストダウンを行うことができます。上記は、軸部分に高さが必要…
→解決事例を見る
-
(5)金型代を抑えられる寸法許容精度にて設計を行う
【Before】
精密なプレス金型を用いた絞りを行うと、±0.05と非常に高い寸法精度で加工を行なうことが可能です。ところが、絞り加工を行なう精密板金加工品においては、すべてが高精度に加工をする必要がない場合があります…
→解決事例を見る
8. 精密板金VA提案コラム
VA提案コラム一覧
9. 精密板金のことならおまかせ下さい!
いかがだったでしょうか?
ここまで、精密板金について詳しく説明させていただきました。
以上のように、精密板金とは金属板に曲げや溶接などの加工を高い精度で行い、機械や装置の部品を作る技術です。精密板金は、小~中ロットでの試作や複雑な形状の製品の加工に向いています。
さらに当社の加工技術「ダイレスフォーミング」なら、一般にプレス板金でしか加工できない複雑な形状の製品でも、金型なしで製作可能。大幅なコストダウンと納期短縮が実現できます。
板金部品のコストや納期にお困りの方は、お気軽に当社までご相談ください。
-
筐体 精密板金
筐体の精密板金における設計のポイント
- 1.溶接、リベット等、最適な結合方法を検討する
- 2.求められる強度を考慮した上で、流通性の高い材料・板厚を使用する
- 3.R 仕上げは「溶接R 仕上げ」を採用する
- 4.ハーフシャー(ダボ)を採用し位置決め時間を低減する
>>詳細はこちら
-
ホッパー 精密板金
ホッパー 精密板金の製作・設計のポイント
- 1.高精度な曲げ加工
- 2.歪み・段差を抑えた溶接加工
- 3.3D‐CAD使用によりリードタイムの削減
>>詳細はこちら
-
カバー 精密板金
カバー 精密板金 コストダウンのポイント
- 1.TIG・ファイバー・スポット・リベットから最適な結合方法を選択する
- 2.R曲げは、きりの良い数字のRであると、コストダウンにつながる
- 3.板厚はなるべく同じ厚さのものを採用する
- 4.塗装範囲を明確にする
>>詳細はこちら
-
タンク 精密板金
タンクの精密板金における設計のポイント
- 1.ビードの数・ピッチなど、溶接の指示を細かく行う
- 2.ワークサイズを考慮して板厚を一定以上にする
- 3.タンク内の流動性を鑑みて、底面に傾斜をつけるなどの工夫を施す
>>詳細はこちら
-
フレーム 板金加工
フレームの板金における設計のポイント
- 1.曲げ構造にてフレームを設計することで、コストダウン
- 2.強度を考慮した上で、部位毎に最適な加工方法を選択する
- 3.図面の展開は板金加工業者に委託する
>>詳細はこちら